Rating a cooler or condenser utilizing AX Sections follows
the method generally accepted for other types of heat transfer
equipment, since the same physical and thermodynamic laws apply.
Knowing inlet and outlet process temperature, quantity of process
fluid, its heat content (either specific or latent, or both),
and quantity and summer temperature of the available cooling water,
the duty is calculated in BTU/hr:
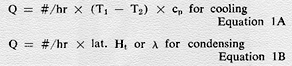
The water temperature rise and final water temperature are then
obtained as follows:

With all terminal temperatures known, the logarithmic mean temperature
difference is found by determining the terminal differences (noting
whether flows are countercurrent or concurrent) and applying the
formula:
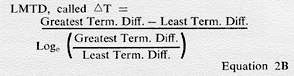
A trial overall heat transfer rate Ut is
selected and the basic heat transfer equation is solved for a
tentative figure for surface.

From this tentative value of S, the number of Sections of the
desired type can be obtained from values for external surface.
With this number of Sections a trial arrangement is made, taking
into consideration various limiting factors of dimension and flow
quantity.
The pressure drop of this trial unit can then be determined from
the appropriate curve, properly corrected for the physical characteristics
of the fluid being cooled. In turbulent flow the pressure drop
varies as the .26 power of the viscosity, as the 1.77 power of
the velocity and inversely as the density. A correction for tube
wall viscosity is also applicable.
Thus:
Having determined the pressure drop, and made whatever adjustments
in arrangements are necessary to bring the figures in line with
the specified requirements, the actual available heat transfer
rate can be calculated from the curve, which represents the basic
heat transfer relationship,
First a value for mass velocity is determined:
then a figure N, the Reynolds number is calculable in convenient
units.

|
Using this value of N, a reading from the curve is employed in
the following formula to give a film rate "hi"
for the fluid flowing inside the sections.
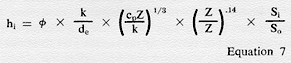
This value of hi is then combined with
inside and outside fouling factors, the resistance of the Section
wall, and the outside film transfer rate, from values given in
the accompanying table.
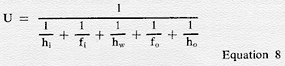
The fouling factors are generally used where no abnormal operating
conditions exist, and are not to be considered inflexible.
After applying the value of U obtained from Equation 8 to the
basic formula in Equation 3 the validity of the original trial
rate is confirmed or disproved. The arrangement, type and number
of Sections can be adjusted to make the most economical unit and
the values of P and U
rechecked.
In determining the number of stacks in a spray installation (not
fully evaporative as described below) the quantity of cooling
water per stack must be considered. For Type AX Sections, this
should be held between 12 and 42 GPM. Maximum stack height should
not exceed 33 Sections except for unusual conditions, although
20 is normal maximum for acid coolers.
If design conditions dictate more than one stack in series per
parallel stream, a correction must be made in the log mean temperature
difference (see Equation 2B). If the flow in each stack is countercurrent
with the water, the following method is used to find the Correct
LMTD:
Water quantity over each stack may be safely assumed to be equal.
The overall U should be nearly constant with no change of state,
and equal surface must be designed into each stack. For other
conditions, the zoning can be worked out most simply by a cut
and try procedure.
The temperature of the hot fluid leaving the first (hottest)
series pass (Tx) is found as follows:
where n is the number of stacks in series.
The temperature of the water leaving this stack tx
is found by determining the duty performed in this first pass
in the manner explained by Equations 1A and 2A. It may be that
a maximum water temperature in the system will be established
as a limit, this could affect the design at this point.
Knowing values of T1, TX,
t1, and TX, all
temperatures for the first pass, use Equation 2B to determine
the LMTD, for this pass.
Then the Corrected LMTD can be found as follows:

|